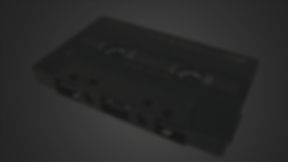
Tape Deck Setup and Alignment
Analog tape decks can sound very good indeed, if they are set up and aligned correctly. If not, they can sound bad and can even damage your tapes. This work is a specialty of mine, and without trying to create a primer on how magnetic recording works (that's a subject for a future webpage), I'd like to share with you some of the intricacies of making these machines sing.
​
The two most common analog tape formats used in High Fidelity systems are the Compact Cassette (more commonly known simply as "cassette," and the reel-to-reel or "open reel" systems. Both formats use the same basic principles for recording and playing back sound, and they share a number of areas that must be attended to if proper operation and good sound are to be expected of them. Open reel decks often have a few extra setup requirements beyond those of cassette decks.
​
The first thing I look at when evaluating a tape deck is the tape path. The tape path is simply all the parts of the tape deck that actually touch the recording tape. The heads, which are the most critical parts of the tape path, are the small electromagnets that erase, record, and play the audio on the tape. The heads must be clean, demagnetized, and not excessively worn. They must also be mechanically aligned with great precision in order to work correctly. Demagnetization is important because the music on your tapes is stored in the form of magnetic fields, and if any part of the tape path is magnetized it can partially (or completely) erase your tapes!
Once I have ascertained that the tape path and heads are or can be made to be in good shape, the next order of business is the transport. The transport is the collection of mechanisms and electrical circuits that move and handle the tape, and the tape path and heads are part of that larger system. The transport must move the tape smoothly and gently at all times, must operate at the correct tape speed and tension at all times, and it must do these things reliably. There are many parts involved that must be checked, including motors, belts, idlers, pulleys, clutches, sensors, switches, guides, levers, bearings, capstan(s) and pinch roller(s), and associated control electronics. In vintage machines, the rubber components (usually belts, pinch rollers, and idler tires) are always suspect, as both natural and synthetic rubber materials degrade and decompose with age. On older, less-expensive open reel machines there may also be pressure pads, which are felt pads used to hold the tape against the heads. These are not used on higher-quality machines. On cassette decks, the pressure pads are part of the cassette tape itself, not the machine.
​
Once the transport is in good order, mechanical alignment can proceed. This involves:
​
1. Setting the height, azimuth, and zenith of the record and play heads, and the height and zenith of the erase head.
2. Adjusting the guides.
3. Setting the tape speed.
4. Checking and adjusting the back tension (the tension placed on the tape as it comes off the feed reel).
5. Checking and adjusting the take-up tension (the tension used to spool the tape onto the take-up reel).
6. Checking and adjusting the fast wind tension (the tension used to fast-forward and rewind the tape).
7. Checking and adjusting the fast-wind back tension (the tension placed on the tape by the reel it is being fast wound off of).
8. Adjusting the pinch roller pressure.
9. Testing and adjusting the functionality of the end-of-tape autostop mechanism, if it exists.
10. Testing and adjusting the functionality of the autoreverse system, if it exists.
Some of these adjustments are interactive, and so they must be repeated until they are all within factory spec. Note that on cassette decks the tape guides are usually attached to the heads and/or are part of the cassette tape itself, and not all machines allow adjustment of all these items. Tension measurements are made using special tension gauges made for the purpose, and the correct settings are usually to be found in the service manual for the machine in question. If a service manual is not available, or if it does not give specific tension specifications, experience will provide a competent technician with a guide for setting these adjustments.
As for tape speed, I'm a bit of a stickler. Most service manuals specify that the tape speed can be off by as much as 1% either way. That's about 1/6 of a semitone for you musicians out there, and that's more error than I care to deal with. I always try to adjust the tape speed to be within 0.25% of perfect, on those machines whose speed is adjustable. Setting the speed with more precision than +/- 0.25% is not only difficult, it is useless, because nearly all machines vary their speed by that much or more when tested at the beginning versus the end of a tape. The exception to my 0.25% accuracy policy is auto-reverse cassette decks, which usually do not (and cannot) run at the same speed in both directions. Those I try to get as close as possible in the forward direction and then let the reverse direction fall where it may. Auto-reverse cassette decks - with the sole exception of the Nakamichi "unidirectional autoreverse" decks - are studies in compromise anyway, and cannot be relied upon for high sound quality.
Some machines, specifically those machines which base their speed off the AC power line frequency, cannot have their speed adjusted. Fortunately, these are often very close to being perfect in speed, provided the transport is in good working order.
​
You've probably heard of "wow and flutter." These are terms describing cyclical variations in tape speed that should not be there. "Wow" is a slow variation up and down that sounds like someone turning turning a pitch control up and down once or twice a second. "Flutter" is a fast variation that sounds like vibrato in a singer's voice. The best test short of a test tone on a professionally-made alignment tape is a recording of a piano with sustained tones.
All analog tape machines have some wow and flutter, but in all but the cheapest (or oldest) machines it is so small as to be inaudible. If it is audible in a good quality machine, the problem must be tracked down and solved. As for wow-and-flutter specifications, anything under 0.1% WRMS (Weighted Root Mean Square, a method of computing the figure in the specification) should be inaudible except to the most highly sensitive ears.
​
At this point, electronic alignment begins. First, a calibrated tape is used to set the playback levels, VU meter readings and equalization. A similar tape would also have been used earlier to adjust the azimuth and tape speed. These tapes are made one at a time by hand and are very expensive, so one does not place them in/on a machine until one is sure the transport works perfectly and that the tape path has been cleaned and demagnetized, for fear of damaging the test tape. Alignment tapes for cassette decks run between $60 and $200, and for open reel they can range between $100 and $1,500. Playback alignment is critical for two reasons: One, it will determine what pre-recorded tapes sound like, and two, the playback function is used to set up the record function. If the playback is not right, the recording alignment will not be right.
​
Once the playback function is made as perfect as possible, the record function is aligned. It is necessary to have the client choose exactly what type of blank tape he or she wishes to use most of the time, because settings that result in the best response for say, TDK SA tape, will not result in the best response for say, Maxell UDXL II tapes, even though both are "Type II," or "Chrome" tapes. Once a tape type is chosen and a sample of that tape has been obtained, the record alignment can begin. First, the bias is set. Bias is an ultrasonic sine wave, usually 100 - 150kHz, to which the audio signal is added before being sent to the record head. The bias is much stronger than the audio signal, and its purpose is to eliminate the terrible distortion that would be caused by attempting to record audio without it. The precise level of bias is critical because it also affects the high frequency response of the tape. Too much bias and the highs disappear, too little and the highs are sharp and ragged, with excessive distortion. Once the bias has been set, the record levels and equalization can be set up. The bias and record level settings are interactive, and must be repeated until both the levels and frequency response are within acceptable limits.
​
After all this comes the listening test. The goal is to have the playback sound as indistinguishable as possible from the original signal. Sometimes, mostly with cassette decks, the settings that result in the best measured response do not result in the best sound. At that point, it would be a choice for the client to make as to whether I leave the settings alone or adjust them for the best perceived sound quality. This almost never happens with open-reel machines.
​
Even this rather long description is nothing more than a summary of what a competent tech does when setting up and aligning a tape deck. That's why it's not cheap to have this done, and it's also why a deck that is set up and aligned properly can sound so good.
At the bottom of this page is a 96 kHz flac recording of the first two minutes of Donald Fagen's song "I.G.Y." from his amazing 1982 album "The Nightfly." This was digitally transferred using my own personal Pioneer CT-F900 cassette deck, playing a 38-year-old pre-recorded cassette. This content is posted under the Fair Use clause of the copyright law, and is intended to educate you about the sound quality achievable when a quality deck is professionally set up and aligned. And yes, the Dolby noise reduction was turned on! You should use good headphones or speakers with an external DAC for best results.
​
And for those of you wondering, "what about eight-track players?," yes, I work on them too. But I only work on component decks made by reputable High Fidelity manufacturers, not tabletop systems made by the likes of Soundesign and Sears. Of course, eight-track decks can never achieve the fidelity of even a mid-level cassette deck due to the numerous compromises in design used to achieve the simplicity of the format. Some of them, though, like models by Marantz, Pioneer, and Pioneer subsidiary Centrex, can sound surprisingly good after a thorough massaging.
​
​
​